La formation QRQC, ou Quick Response Quality Control est un outil essentiel. Elle est importante pour les entreprises cherchant à :
- améliorer leur performance ;
- respecter les exigences des référentiels normatifs tels que les normes ISO, IATF 16949, EN 9100, ISO 13485, …
En développant les compétences de vos équipes en QRQC, vous pouvez :
- améliorer la qualité de vos produits et services ;
- réduire les coûts et les délais ;
- augmenter la satisfaction de vos clients.
Dans cet article, nous allons explorer tout ce qu’il y a à savoir sur le QRQC Quick Response Quality Control.
Sommaire
ToggleQu’est-ce que la formation QRQC ?
La formation Quick Response Quality Control est un programme de développement des compétences. Elle enseigne aux équipes les principes et les outils de la méthodologie QRQC.
Celle-ci vise à résoudre rapidement et efficacement les problèmes de qualité. Elle identifie et élimine les causes racines.
Le Quick Response Quality Control est basé sur une approche structurée et systématique. Il implique l’utilisation :
- d’outils d’analyse ;
- de techniques de résolution de problèmes.
Grâce à leurs acquis, ils vont pouvoir résoudre des problèmes réels et trouver rapidement un système de gestion de la qualité efficace dans leur entreprise.
Les bases du QRQC
Le QRQC est basé sur :
- l’implication des opérateurs en charge de la détection des défauts ;
- l’intervention des services supports ;
- la rapidité.
Avec l’aide des opérateurs, ils vont :
- faire une analyse ;
- chercher une cause potentielle ;
- procéder au traitement ;
- engager les actions.
Historique et évolution
Le QRQC a été développé dans les années 1970 par Kaoru Ishikawa, un ingénieur japonais employé chez Toyota. Il a notamment créé le diagramme Ishikawa, connu également sous le nom de diagramme causes-effets. Cet outil peut aider à identifier les causes racines des problèmes qualité.
Le QRQC a évolué au fil des ans pour inclure de nouveaux outils et techniques tels que :
- les 5 Pourquoi ;
- le PDCA ;
- la méthode 8D.
Aujourd’hui, le QRQC est utilisé dans de nombreux secteurs, notamment :
- l’automobile ;
- l’aérospatiale ;
- la santé ;
- l’électronique.
Principes fondamentaux
Les principes fondamentaux du QRQC comprennent :
- l’identification des problèmes ;
- une analyse immédiate ;
- des actions correctives rapides ;
- une évaluation des résultats ;
- une amélioration continue.
Avantages de la méthodologie QRQC
Les résultats obtenus grâce au QRQC sont nombreux dont l’amélioration :
- de la qualité ;
- des produits ;
- des processus.
Cela se fait en éliminant ou en réduisant les sources d’erreur ou de défaillance.
Cet outil contribue à la réduction des coûts liés à la non-qualité qui incluent les :
- rebuts ;
- retouches ;
- frais de garantie ;
- pénalités.
L’optimisation des performances opérationnelles est décisive. Elle se traduit par une augmentation de la :
- productivité ;
- capacité ;
- flexibilité.
Amélioration continue
L’amélioration continue est au cœur du QRQC. Elle vise l’optimisation des processus et intègre tous les niveaux de l’entreprise.
Réduction des coûts et des délais
En identifiant et en éliminant les causes racines des problèmes de qualité, les entreprises peuvent réduire les coûts. Ces derniers sont associés aux :
- rebuts ;
- retouches ;
- retards de livraison.
Maintenant que nous connaissons la valeur de la méthode QRQC pour l’entreprise, voyons ci-après comment la mettre en place au sein de l’organisation interne.
Étapes clés de la mise en œuvre du QRQC dans une organisation
Les étapes clés dans la mise en œuvre d’un QRQC dans une entreprise sont multiples.
Elles commencent par la préparation et la planification. Ces premières phases comprennent une évaluation des besoins et des objectifs. Ensuite, il y a le choix d’une équipe avec l’aide d’un expert qualité, peut-être d’un chantier pilote, et des outils.
Le processus se poursuit avec le déploiement et l’application. Cette phase intègre :
- la formation des équipes ;
- le suivi ;
- l’ajustement ;
- le partage des acquis du chantier pilote dans les autres secteurs.
Préparation et planification
Pour lancer le QRQC dans une entreprise, il est nécessaire de commencer par identifier :
- un chantier ;
- une équipe ;
- un secteur pilote.
Secteur pilote veut dire domaine dans lequel nous pensons que les gens vont adhérer. Nous espérons y avoir un succès plus facile que dans un autre. Lorsque ce chantier aura été une réussite, nous pourrons déployer l’outil dans les autres secteurs.
Dans cette étape, il faut également définir le support des QRQC (paperboard, cahier, …). Ensuite, il faudra l’enregistrer dans le système de management des informations documentées de l’entreprise.
Évaluation des besoins et objectifs
L’évaluation des besoins et objectifs de l’entreprise permet de déterminer les domaines prioritaires pour la mise en place du QRQC. Cela peut inclure :
- l’identification des problèmes qualité les plus courants ;
- l’analyse des coûts associés à ces problèmes ;
- la définition des objectifs d’amélioration.
Une planification de déploiement est intégrée dans le projet. Celle-ci est, une fois de plus, basée sur deux points :
- un démarrage dans un secteur pilote ;
- un déploiement sur l’ensemble des autes secteurs de l’entreprise.
Choix de l’équipe et des outils
Le choix de l’équipe et des outils est d’une importance capitale pour la réussite de la mise en place du QRQC.
Tout cela est la clé du succès.
Lancer un outil comme le QRQC sur un chantier pilote présente des risques. Celui-ci sera regardé par d’autres secteurs. S’il échoue, cela va être très préjudiciable au déploiement de la méthode dans les autres domaines par la suite.
Déploiement et application
Pour déployer l’outil, nous allons commencer par créer le support d’enregistrement du QRQC. Les instructions éventuelles qui permettront de l’expliquer sont à afficher :
- dans l’atelier ;
- dans les services où la méthode sera déployée.
Il va falloir ensuite :
- former la première équipe pilote ;
- l’accompagner pour le déploiement ;
- faire un premier bilan.
Puis, il est important de communiquer autour de ce bilan. Cela permettra de déployer la méthode ailleurs.
Formation des équipes
Les équipes vont devoir être formées aux étapes principales de la méthode, à sa conduite mais aussi à ses principes structurants par le biais d’une formation de responsable qualité.
Cinq principes guident le comportement des acteurs impliqués.
La rigueur est le premier. Il s’agit de respecter les :
- règles ;
- procédures ;
- standards établis.
Le deuxième principe est l’attitude ou san-gen-shugi. Il s’agit d’une expression japonaise qui signifie « aller à la source ». Elle implique plusieurs actions :
- se rendre sur le lieu du problème, le genba ;
- observer le produit ou le processus concerné, le genbutsu ;
- collecter les faits et les données réelles, le genjitsu (speak with data).
Le management visuel est le troisième principe. Il s’agit d’utiliser des outils visuels tels que des :
- tableaux ;
- graphiques ;
- indicateurs.
Ils permettent d’afficher les informations relatives aux problèmes et aux actions correctives. Pour les différents acteurs, ces outils facilitent :
- la communication ;
- la coordination ;
- le suivi de l’avancement et des résultats des actions correctives ;
- la transparence.
Le dernier principe est l’escalade. Il consiste à remonter les problèmes et les actions correctives au niveau hiérarchique supérieur. Cela se fera uniquement :
- si le délai imparti est dépassé ;
- si le problème dépasse le périmètre de la compétence du niveau concerné.
Cela permet de mobiliser les ressources nécessaires et d’accélérer la résolution des problèmes.
Suivi et ajustements
Le suivi et les ajustements sont nécessaires pour assurer la réussite à long terme de la mise en place du QRQC.
Dès le chantier pilote et le lancement dans chacune des autres équipes, plusieurs actions sont requises. Il va falloir :
- suivre les progrès réalisés dans la résolution des problèmes qualité ;
- mesurer l’efficacité et les solutions mises en œuvre ;
- apporter les ajustements nécessaires.
Surtout, il est important de s’assurer :
- que les équipes ne s’essoufflent pas ;
- que l’outil n’est pas mis de côté par manque d’encadrement.
Outils et techniques spécifiques de la QRQC
Le QRQC va s’appuyer sur un support, un formulaire, un paperboard, un document d’enregistrement. Ce document va comprendre plusieurs parties :
- le QQOQCPC (qui, quoi, où, quand, comment, pourquoi, combien) pour identifier le problème de façon complète ;
- les 5 Pourquoi, pour remonter à la cause racine à partir d’une cause directe ;
- le PDCA, pour planifier les actions décidées dans le groupe, déployer, les contrôler et réagir en cas de besoin ;
- la mise à jour des standards et du plan de surveillance.
Outils d’analyse des causes racines
Pour identifier les causes racines, il est nécessaire de commencer par la détection des causes directes. Pour cela, le diagramme d’Ishikawa sera d’une aide précieuse.
Ensuite, il est important de remonter des causes directes retenues aux causes racines en utilisant la méthode du 5 Pourquoi.
Diagramme Ishikawa
Le diagramme Ishikawa, est également connu sous le nom de diagramme cause-effet, diagramme arête de poisson ou 5M pour :
- méthode ;
- milieu ;
- moyen ;
- main d’œuvre ;
- matière.
Il permet d’identifier des causes directes des problèmes qualité.
5 pourquoi
Une fois la cause directe d’occurrence identifiée à l’aide de l’Ishikawa, nous allons devoir remonter aux causes racines. L’outil 5 Pourquoi va permettre de le faire. Il consiste à poser cinq fois de suite la question Pourquoi.
Une fois que nous pensons être arrivés à la cause racine, il est temps de s’assurer que notre démarche est logique. L’idée est de repartir de la cinquième cause, en passant la quatrième, la troisième, etc. en remontant, en insérant le mot « donc » entre elles.
Techniques de résolution de problèmes
Lorsque les causes racines sont identifiées et connues, il est temps de définir les actions, avec ou sans la contribution d’un consultant qualité. Ces dernières vont nous permettre de résoudre le problème en supprimant les causes racines validées.
PDCA (Plan-Do-Check-Act)
L’outil pour planifier et engager les actions va être le PDCA, donc un plan d’action sous la forme suivante :
- Plan : définir ce qu’il faut faire ;
- Do : enregistrer la date à laquelle cela a été fait ;
- Check : vérifier l’efficacité ;
- Agir : améliorer en fonction du résultat.
8D
Le 8D est une méthode structurée pour résoudre les problèmes qualité. Il comprend 8 étapes :
- première étape : créer une équipe de travail ;
- deuxième étape : décrire de façon précise le problème ;
- troisième étape : confiner le problème en maîtrisant les risques de récurrence jusqu’à ce que les actions correctives soient validées ;
- quatrième étape : identifier les causes racines ;
- cinquième étape : planifier et mettre en œuvre les actions décidées ;
- sixième étape : évaluer l’efficacité de ces actions ;
- septième étape : transversaliser l’action validée à tous les cas similaires où le problème pourrait se poser et standardiser dans les documents du système ;
- huitième étape : communiquer et féliciter l’équipe.
Étude de cas et retours d’expérience
Les études de cas et les retours d’expériences sont utiles. Ils servent à :
- comprendre les avantages et les défis de la mise en place du QRQC dans l’entreprise ;
- partager des choses qui se sont bien ou mal passées ;
- éviter de reproduire les mêmes erreurs.
Success stories d’entreprises ayant implémenté le QRQC
Parmi les nombreuses entreprises qui ont réussi à améliorer leur performance grâce à la mise en place du QRQC, nous pouvons noter par exemple :
- Toyota, pour réduire les coûts de production et à améliorer la qualité de ses véhicules ;
- General Electric, pour améliorer la qualité de ses produits et réduire les délais de livraison ;
- l’équipementier Valeo, qui suite à l’impulsion donnée par son directeur qualité japonais, Kaoru Kawashima, a déployé cet outil dans tous ses sites et a formé l’ensemble de sa supply chain, de ses fournisseurs à l’outil.
Impacts sur la qualité et la performance
Les impacts sur la qualité et la performance peuvent être significatifs. Cela se vérifie lorsque le QRQC est mis en œuvre correctement.
Une étude de cas menée par l’université de Malaya a montré des résultats importants. La mise en œuvre du QRQC dans une entreprise de fabrication de semi-conducteurs a entraîné la réduction de 50% des défauts de production.
Témoignages et conseils pratiques
Les témoignages et les conseils pratiques peuvent aider les entreprises à comprendre les défis et les avantages de la mise en place du QRQC.
Erreurs courantes et leçons apprises
Deux erreurs principales reviennent souvent dans la mise en place d’un QRQC.
La première, c’est de ne pas réfléchir suffisamment :
- à l’équipe pilote ;
- au secteur pilote dans lequel l’action va être lancée.
La deuxième erreur serait de ne pas faire le suivi du déploiement suffisamment longtemps. Elle a été constatés dans quelques entreprises qui ont été accompagnées par QSE Perf.
Après un lancement réussi, l’outil a été délaissé quelques mois ou trimestres après. Les opérateurs, ou plutôt les équipes, avaient du mal à faire venir au pied des machines les services supports.
Les opérationnels n’aimaient pas forcément écrire et formaliser. Devant l’absence de réaction, ils ont assisté à l’abandon progressif de l’outil.
Challenges et obstacles
Les challenges et les obstacles courants lors de la mise en œuvre du QRQC comprennent :
- la résistance aux changements ;
- le manque de temps et de ressources ;
- la difficulté à identifier les causes racines des problèmes de qualité.
Recommandations pour une mise en œuvre réussie
Les recommandations pour la mise en place réussie du QRQC comprennent :
- la formation en qse des équipes ;
- l’implication de la direction de l’entreprise ;
- la sélection appropriée des projets QRQC ;
- la mesure régulière des résultats et l’ajustement des actions en conséquence.
Il est très important de faire comprendre aux équipes que le QRQC est un outil d’amélioration continue.
La question est de savoir : est-ce vraiment certain que c’est ce clou-là qui a accroché votre chemise ? Peut-être pas. Cependant, celui-là ne fera plus de mal à personne et c’est le principe même du QRQC.
Le but est d’arriver à faire comprendre cela à l’ensemble des personnes impliquées. Elles comprendront par la suite qu’elles sont dans une démarche d’amélioration continue. En ayant compris l’intérêt de cet outil, elles auront plus de mal à stopper son utilisation.
Foire aux questions
Combien de temps dure généralement une formation QRQC ?
Une formation Quick Response Quality Control peut avoir une durée variable. Cela va dépendre de l’objectif et du niveau. Elle peut varier de quelques heures à quelques jours.
Après la formation, il faudra assurer un suivi du déploiement. Celui-ci pourrait être de plus en plus espacé, mais ne doit pas s’arrêter trop rapidement.
La formation QRQC est-elle adaptée aux débutants ?
Une formation en QRQC est adaptée à tous les niveaux, qu’il s’agisse de personnes expérimentées ou de débutants. Elle n’a pas de prérequis exigés. Cette formation permet de comprendre la philosophie d’apporter des bases solides.
L’entreprise s’améliore si, en cas de problème, tout le monde :
- se mobilise au service de la production pour le résoudre ;
- intervient rapidement sur le lieu de sa survenance.
La formation QRQC inclut-elle des études de cas pratiques ?
Comme toutes les formations notamment animées par QSE Perf, celle en QRQC incluent évidemment des études de cas pratiques. Les apprenants vont être mis en situation réelle afin qu’ils puissent concrètement :
- appliquer la méthode ;
- valoriser l’outil ;
- ancrer l’apprentissage.
Comment mesurer l’efficacité d’une formation QRQC dans une organisation ?
L’efficacité d’une formation Quick Response Quality Control se mesure de différentes manières :
- comparer les performances qualité avant et après la formation ;
- surveiller les indicateurs clés : qualité, délais, coût selon la nature des problèmes traités ;
- prendre en compte le feedback des participants, leur évaluation à chaud ou à froid ;
- voir l’impact sur la résolution des problèmes.
Le plus important est de mesurer cette efficacité sur le moyen et le long terme.
L’erreur serait :
- de valider l’efficacité d’une formation après une mise en place initiale satisfaisante ;
- de passer à côté du fait que la démarche s’épuise et finit par être abandonnée.
Peut-on suivre une formation QRQC à distance ?
Une formation QRQC à distance est possible. A titre d’exemple, QSE Perf l’a déployé notamment lors de la période de confinement au moment de la COVID-19. Elle permet de réaliser :
- des exercices ;
- des cas pratiques.
Toutefois, elle sera probablement moins concrète qu’une formation en présentiel dans l’entreprise. Cette dernière est plus intéressante car, avec le groupe, elle permet d’appliquer la méthode sur des cas réels, notamment les derniers incidents détectés en production.
En savoir plus
https://www.info-industrielle.fr/automobile/controle-qualite-entreprise-qrqc/
https://blog.operaepartners.fr/2017/07/12/le-qrqc-cest-quoi/
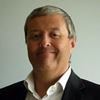
François Pobelle a obtenu son diplôme d’ingénieur mécanique en 1986 à l’école nationale d’ingénieurs de Belfort (ENIB devenue UTBM). Puis, il a enrichi sa formation en se spécialisant en management à l’I.A.E. de Dijon pour obtenir un MBA en gestion en 1988.
Recruté par « Pratic » à l’issue de son stage de fin d’études en management, il s’est vu confier un an plus tard le premier audit de Peugeot pour la mise en place de la première version du référentiel d’évaluation d’aptitude qualité fournisseur (EAQF). Ce projet a marqué ses premiers pas dans le monde des systèmes de management qualité.
Par la suite, désigné pour piloter le système Qualité du groupe devenu « EM Technologies », il a obtenu les certificats ISO/TS 16949, ISO 14001 et OHSAS 18001 pour les différents sites.
Son aventure avec ce groupe, devenu « Maike Automotive », s’est achevée en 2018. Néanmoins, sa passion pour les systèmes de management est restée intacte et l’a inspiré à fonder QSE Perf, axé sur l’audit et l’amélioration des entreprises.